What is a Written Silica Dust Control Plan?
If you’re not familiar with this, perhaps we should start with the basics. What is silica? Silica is the most common mineral on earth; it can be found in soil, sand, concrete, natural stone, tile, etc. In those forms, silica doesn’t generally pose any risks. However, when those materials are cut, ground, polished, or crushed then respirable crystalline silica may be released.
Respirable crystalline silica dust is up to 100x smaller than the grains of sand. These particles are so fine they get trapped in your lungs, and despite their tiny size they are sharp and cause your lungs to create scar tissue. Over time, this can cause silicosis and other health problem. OSHA released updated standards for exposure to silica dust in the workplace in 2017, and one of the requirements was for a Written Exposure Control Plan.
Who needs a Written Silica Dust Control Plan?
Anyone who does masonry or hardscaping work will need one. Those working in quarries, granite countertops, poured concrete, or similar work would also need a plan. Any company whose work would expose employees to respirable crystalline silica needs to have a Control Plan.
What does a Written Silica Dust Control Plan include?
- The Written Control Plan will list all the tasks that will expose workers to respirable crystalline silica.
- Each task should list the specific engineering controls, work practices, and respiratory protection that are required.
- Housekeeping rules should also be included. In general, dry sweeping or using compressed air are not permitted for cleaning up dust containing respirable crystalline silica. Acceptable methods such as vacuum, wet sweeping, etc. should be detailed.
4. If tasks will generate enough silica dust that respirators are required, the plan should detail how access to the work area will be restricted.
Learn more about our 7 Step Training Plan to Silica Dust Control below.
Who needs access to the Written Silica Dust Control Plan?
Employees, their agents (such as attorneys or union representatives), and safety inspectors all need access to the control plan. Employees should fully understand the control measures and how to implement them.
Ideally, there should be a copy available on the jobsite as well as in the office. Thus, it is readily available to both employees and any inspector, whether they visit the office or the jobsite.
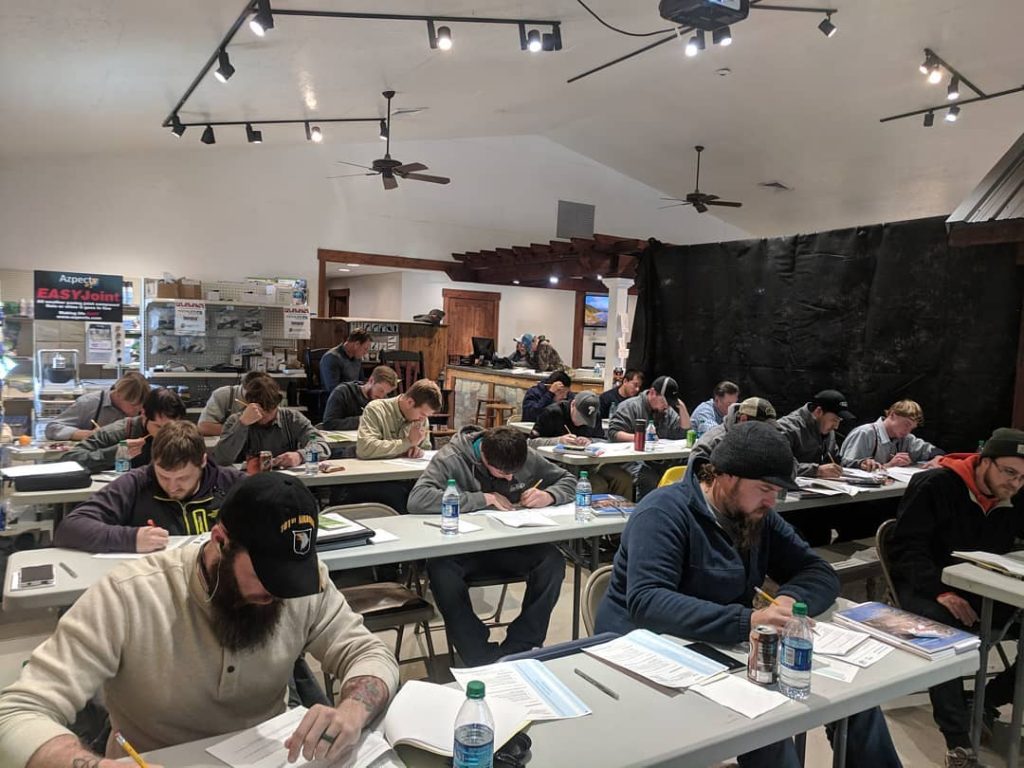
Classes discussing a proper silica dust control plan are also offered to teach anyone who desires about hardscaping and the effects of silica dust entering the body. You may contact us directly or view our events page to see if there is an event going on near you.
The plan should be reviewed annually, and the effectiveness of the measures evaluated. This review is required to keep the plan up-to-date. The company may have begun completing different types of work with varying exposures to respirable crystalline silica. New equipment may have been added, again that may have varying exposure levels and control measures.